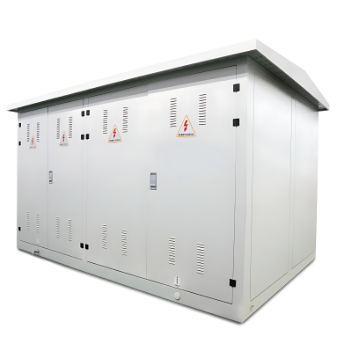
1. Challenges and Innovative Solutions
Despite significant advantages, compact substations still face technical challenges in practical applications. Performance optimization requires innovative solutions.
1.1 Thermal Performance Optimization
- Core Issue:Heat accumulation effect of equipment in enclosed space
- Innovative Solutions:
- Directed Airflow Technology:Establishing independent air ducts (dedicated transformer-radiator channels), avoiding heat exchange interference; improves heat dissipation efficiency by 40%.
- Phase Change Material (PCM) Application:Filling cabinet walls with microencapsulated PCM (melting point 45°C) to effectively buffer temperature spikes.
- Intelligent Control System:Staged ventilation activation (natural ventilation at 40°C → forced ventilation at 50°C → air conditioning cooling at 60°C).
1.2 Overcoming Space Constraints
- Core Issue:Conflict between functional density and maintenance accessibility within limited space.
- Innovative Solutions:
- 3D Layout Optimization:Adopting Z-shaped busbar arrangement, improving vertical space utilization by 30%.
- Modular Sliding-out Design:Circuit breaker modules equipped with rail systems, allowing entire unit to slide out for maintenance.
1.3 Initial Investment Control
- Core Issue:Prefabrication increases the proportion of equipment costs.
- Innovative Solutions:
- Modular Tiered Configuration:Basic Type (essential functions) / Enhanced Type (+smart monitoring) / Advanced Type (+capacity & voltage regulation).
- Financial Model Innovation:EPC + Energy Performance Contracting, amortizing equipment premium through energy savings.
- Standardized Design:Establishing a library of 12 standard solutions to reduce non-standard design costs.
1.4 Electromagnetic Interference (EMI) Protection
- Core Issue:Electromagnetic compatibility (EMC) challenge within compact space.
- Innovative Solutions:
- Layered Shielding Technology:Transformer compartment uses a composite structure of μ-alloy (low-frequency shielding) + copper mesh (high-frequency shielding).
- Active Cancellation System:Real-time monitoring and generation of counter electromagnetic fields, achieving field strength suppression of 20dB.
- Topology Optimization:Dyn11 connection combined with star-delta windings, suppressing 3rd harmonic by over 90%.
2. Implementation Pathway Recommendations
Successful compact substation projects require a scientific approach and phased execution of key tasks.
2.1 Planning Phase
- Load Characteristic Analysis:Use smart meter data for 8760-hour load simulation to identify peak/valley characteristics (e.g., a food plant found load <40% Sn for 30% of operating time).
- Scenario-based Selection:
Scenario Type
|
Recommended Model
|
Technical Focus
|
Commercial Center
|
American Compact Type
|
Low noise, landscape integration
|
Industrial Zone
|
European Robust Type
|
High protection, large capacity
|
Renewable Plants
|
Smart Capacity Reg.
|
Fluctuation adaptation, harmonic sup.
|
Rural Grid
|
Simple Economic Type
|
Capacity reg., pollution flashover prot.
|
- Location Optimization:Apply Voronoi algorithm to delineate supply zones, ensuring distance from load center to substation ≤500m.
2.2 Design Phase
- Modular Configuration:Example - Hospital Project:
- Base Unit: 2×800kVA transformers (N+1 redundancy)
- Expansion Module: 125kW emergency power interface
- Smart Kit: Power quality monitoring + fault pre-warning
- Digital Twin Application:Conduct electromagnetic field simulation (ANSYS Maxwell), thermal analysis (Fluent), and structural verification (Static Structural) on a BIM platform to predict design flaws.
- Connection System Optimization:Adopt closed-loop operation (normally open-loop), reducing short-circuit current by 40%.
2.3 Installation Phase
- Foundation Innovation:Precast concrete base (3-day curing) vs. traditional cast-in-place (28-day curing).
- Commissioning Process:Factory pre-commissioning (90% function verification) → On-site joint commissioning (48 hours).
2.4 Operation & Maintenance (O&M) Phase
- Intelligent O&M System:
- Real-time Monitoring Layer:SCADA + IoT platform (5-minute data refresh).
- Analysis & Alert Layer:Lifespan prediction based on equipment degradation models (error <5%).
- Decision Support Layer:Maintenance strategy optimization (reducing O&M costs by 35%).
- Condition-Based Maintenance (CBM) Strategy:Transition from "time-based maintenance" to "data-driven maintenance"; reduced failure rate by 70% in a water plant case.
- Lifecycle Management:Conduct comprehensive performance assessment every 5 years over a 20-year lifespan, implementing energy efficiency upgrades as appropriate.