Single - phase distribution transformers, as crucial voltage transformation and power distribution equipment in the power system, are widely used in rural power grids, low - voltage residential areas, and areas with concentrated single - phase loads. With the continuous increase in the proportion of single - phase loads in the distribution network, the failure rate of single - phase transformers has also increased. Timely identification and handling of these faults are of great significance for ensuring power supply. According to the latest research, the common faults of single - phase distribution transformers mainly focus on five categories: winding faults, insulation aging, oil leakage, abnormal temperature, and low - voltage tap faults. These faults not only interfere with the normal operation of the transformer but may also cause equipment damage and power supply interruptions. This article will comprehensively analyze the causes, characteristics, and handling methods of various faults, providing practical guidance for operation and maintenance personnel of the power system.
1. Winding Faults
Winding faults are the most frequent fault type in single - phase distribution transformers, including inter - turn short circuits, open circuits, and grounding faults of windings. They are mostly caused by insulation material aging, mechanical damage, or manufacturing defects. An inter - turn short circuit in the winding will cause local overheating inside the transformer, accelerating insulation aging, and may eventually lead to the overall damage of the winding. Research shows that when there is a slight short circuit in the transformer winding, traditional devices such as differential protection and gas protection may not operate in the early stage of the fault, placing higher requirements on the fault identification ability of operation and maintenance personnel.
(1) Fault Manifestations
- Abnormal Noise: The transformer emits a "gurgling" sound of oil boiling or a "sizzling" discharge sound.
- Abnormal Temperature: The oil temperature exceeds the standard. When the gas content in the oil exceeds the attention value, the transformer status should be checked immediately (in accordance with IEC standards).
- Resistance Imbalance: The unbalance rate of the DC resistance of the winding exceeds 2% (allowable value), indicating possible winding deformation or poor contact.
- Abnormal Voltage: The output voltage is unstable and drops significantly. Moreover, the low - voltage winding is more likely to deform during a sudden short circuit (the low - voltage winding is more likely to deform under pressure).
(2) Handling Measures
- Emergency Shutdown: Immediately cut off the power supply and stop the transformer operation.
- Precise Detection: Use an infrared thermometer to check the temperature distribution of the winding, locate the fault; measure the DC resistance and capacitance to evaluate the degree of deformation.
- Repair and Replacement: If necessary, lift the cover for maintenance, repair or replace the damaged winding.
(3) Prevention Strategies
- Regular Testing: Conduct winding insulation tests to understand the insulation status.
- Avoid Overload: Strictly prohibit long - term overload operation of the transformer to reduce the risk of winding damage.
- Pre - maintenance Inspection: Conduct preventive inspections before the peak load period to identify hidden dangers.
- Stable Installation: Ensure the transformer is installed firmly to reduce the impact of vibration on the winding.
2. Insulation Aging Faults
Insulation aging is the second most common fault in single - phase distribution transformers, including the aging of solid insulation materials and the deterioration of oil insulation. Insulation aging will reduce the insulation performance of the transformer and accelerate the overall aging of the equipment. According to statistics, it can shorten the designed service life (35 - 40 years) of the transformer to about 20 years, which is particularly prominent in transformers that have been in long - term operation, in harsh environments, or with insufficient operation and maintenance.
(1) Fault Manifestations
- Oil Quality Change: The transformer oil gradually changes from light yellow to orange or brown, and even carbon deposits appear.
- Insulation Decline: The insulation resistance test value is lower than the standard, and the partial discharge volume increases.
- Abnormal Sound: The operation sound is sharp and uneven, and the aging rate is positively correlated with temperature (following the Arrhenius theory, the aging rate doubles for every 6°C increase in temperature).
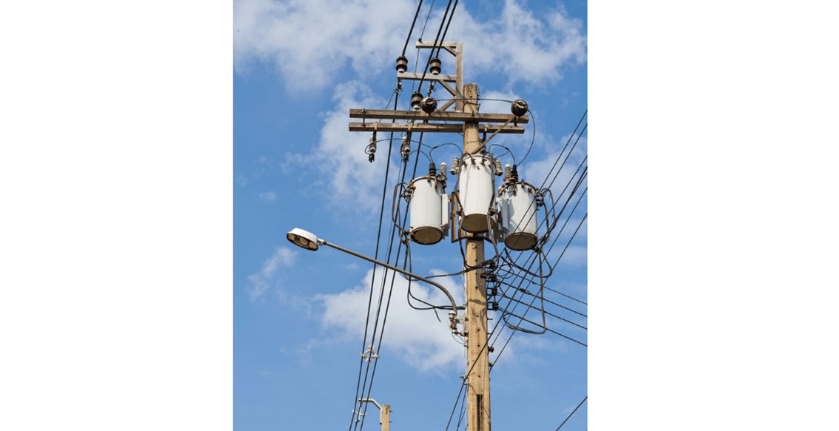
(2) Handling Methods
- Oil Sample Analysis: Conduct chromatographic analysis to detect the content of characteristic gases and judge the degree of aging.
- Oil and Material Disposal: According to the aging situation, decide whether to change the oil, replace the solid insulation material, and conduct a comprehensive overhaul if necessary.
(3) Prevention Strategies
- Regular Detection: Regularize oil quality detection and insulation resistance testing to control the insulation status.
- Temperature - controlled Operation: Maintain a reasonable temperature (GB standard: the average temperature rise of the winding of the oil - immersed transformer ≤ 65°C, and the temperature rise of the top oil ≤ 55°C).
- Environment Optimization: Improve the operating environment, reduce the erosion of dust, humidity, and harmful gases; select high - efficiency transformers such as the S11 type to reduce temperature rise and losses.
3. Oil Leakage Faults
Oil leakage is a frequent and harmful fault in single - phase distribution transformers. It accounts for more than 40% of the faults in power transformers, which will affect the insulation and heat dissipation performance, and cause equipment fire, pollution, and economic losses.
(1) Fault Manifestations
- Oil Level Drop: The oil level gauge shows a decrease in oil level, and oil stains can be seen on the surface of the oil tank.
- Related Abnormalities: The operation sound is sharp and uneven, the oil - paper insulation is damp, and the leakage is aggravated in rainy days and high - humidity environments.
(2) Fault Causes
Aging/damage of seals, weld cracking, improper bushing installation, loose connections caused by vibration, oil tank rust, and abnormal oil pressure caused by a blocked breather.
(3) Handling Methods
- Graded Treatment: Temporarily repair small leaks, and immediately shut down and conduct a comprehensive overhaul for serious leaks.
- Root Repair: Replace seals, repair welds/connections, clean the breather, and ensure the normal operation of the oil conservator.
(4) Prevention Strategies
- Seal Inspection: Regularly check the sealing status, and strengthen fixation in vibrating environments.
- Material Upgrade: Use high - quality sealing materials, clean the oil tank to prevent corrosion; old transformers can be replaced with products with new sealing structures.
4. Abnormal Temperature Faults
Abnormal temperature is a key fault type in single - phase distribution transformers, including winding overheating, local overheating of the iron core, and oil temperature rise. It is the "trigger" for faults such as insulation aging, oil leakage, and winding deformation. According to IEC standards, when the hottest spot temperature reaches 140°C, bubbles will be generated in the oil, which will reduce insulation or cause flashover, damaging the transformer.
(1) Fault Manifestations
- Temperature Exceeding Standard: The oil temperature gauge shows an abnormality, the local surface is overheated and discolored, and the oil level of the oil conservator is abnormal.
- Abnormal Sound: Emits a "buzzing" sound, which becomes louder as the load increases; the oil color becomes darker and carbon deposits appear.
(2) Fault Causes
Transformer overload, internal faults (winding/iron core short circuit), cooling system faults, high ambient temperature, insufficient oil volume due to poor sealing, and poor installation ventilation.
(3) Handling Methods
- Load Reduction and Shutdown: Immediately reduce the load or shut down, and check the cooling system.
- Precise Diagnosis: Use an infrared thermometer to locate the over - heated point, take an oil sample for chromatographic analysis, check for internal faults; repair external causes.
(4) Prevention Strategies
- Monitoring and Analysis: Regularly monitor the temperature, establish a trend analysis; avoid long - term overload.
- Environment Optimization: Optimize the installation position to ensure ventilation; clean the dirt on the heat sink; increase capacity or operate multiple units in parallel in high - load areas, and install sunshades and ventilation devices in high - temperature environments.
5. Low - voltage Tap Faults
Low - voltage tap faults are unique to single - phase distribution transformers, including poor contact, open circuits, and wrong connections. Because the low - voltage side mostly adopts a tap - off design (such as three/four taps), the connection quality directly affects the output voltage and operation stability, which is common in transformers with large load fluctuations and insufficient operation and maintenance.
(1) Fault Manifestations
- Voltage Abnormality: The output voltage is unstable, too high/too low.
- Sound Abnormality: Emits a "clatter" "rustling" mechanical friction sound, which is obvious when the load changes; the voltage on the low - voltage side is unbalanced, and the operation temperature is abnormally high.
(2) Fault Causes
Poor tap welding, oxidation of the contact surface, insecure installation, failure to restore connections during operation and maintenance, large contact resistance caused by a humid environment, and contact point wear caused by load fluctuations.
(3) Handling Methods
- Power - off Maintenance: Check the tap connection, re - weld, and fasten loose parts, replace aging components.
- Cleaning and Protection: Clean poorly contacted parts to ensure good contact of the tap - changing switch.
(4) Prevention Strategies
- Regular Inspection: Regularize the inspection of tap connections, and use high - quality welding materials and processes.
- Environment Adaptation: Strengthen moisture - proof measures in humid environments; for transformers with frequent tap adjustments, replace with reliable connection methods; replace old equipment with products with new tap designs.
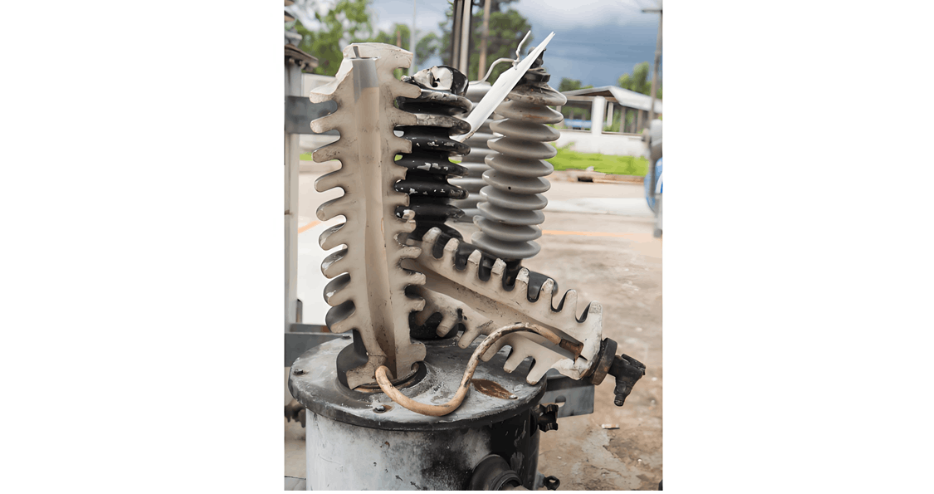
6. Application of Intelligent Monitoring Technology in Fault Diagnosis
With the development of the smart grid, the traditional diagnosis mode relying on manual experience and simple instruments has gradually been replaced by intelligent monitoring technology. The fault diagnosis system based on artificial intelligence can monitor the operation status in real - time, early - warn risks in advance, and improve the accuracy and efficiency of diagnosis.
(1) Mainstream Technologies
- Infrared Sensing Temperature Measurement: With an accuracy of ±1°C, it can accurately detect abnormal temperatures.
- Acoustic Signature Recognition Diagnosis: Analyze the frequency and characteristics of the operation sound to distinguish between normal and fault sounds.
- Analysis of Dissolved Gases in Oil: Detect the content of characteristic gases to determine the type and degree of internal faults.
- Machine Learning System: Integrate multiple parameters to establish a fault prediction model.
(2) Application Effects
After applying infrared temperature measurement, a power company increased the fault detection rate by 65% and shortened the processing time by 40%; acoustic signature recognition can detect winding faults 3 - 6 months in advance. The intelligent system can also locate faults and evaluate the severity, providing a basis for operation and maintenance decisions.
7. Maintenance and Prevention Measures for Single - phase Transformers
Most faults of single - phase distribution transformers are related to long - term operation, environment, and insufficient operation and maintenance. Establishing a scientific maintenance system and implementing preventive measures are the keys to reducing faults and extending service life.
(1) Daily Maintenance
- Oil Condition Inspection: Regularly check the oil level and oil color to ensure the oil level is normal and the oil quality is good.
- Status Monitoring: Monitor the operation sound, monitor the temperature, and establish a trend analysis.
- Component Inspection: Check the cleanliness, damage, and discharge traces of bushings; verify the grounding system (the grounding resistance of 100 kVA and above ≤ 4Ω, and below ≤ 10Ω).
- Environmental Management: Ensure stable installation, clean surface dirt, and prevent pollution discharge.
(2) Classified Prevention
- Winding Faults: Avoid overload and conduct regular insulation tests.
- Insulation Aging: Operate at a controlled temperature and conduct regular oil quality detection.
- Oil Leakage: Regularly check the seal and strengthen fixation in vibrating environments.
- Abnormal Temperature: Optimize installation, ensure ventilation, and install temperature monitoring devices.
- Tap Faults: Regularly check connections, use high - quality welding processes, and prevent moisture in humid environments.
(3) Standard Adaptation and Optimization
Select high - efficiency transformers according to GB20052 - 2020 to reduce losses and temperature rise; operate multiple units in parallel in high - load areas to reduce the load pressure on a single unit; strengthen environmental management to reduce external erosion.
8. Conclusions and Recommendations
The common faults of single - phase distribution transformers are interrelated, and most are caused by a single factor leading to multiple types of fault manifestations. Building a complete fault diagnosis system that integrates traditional experience and intelligent technology can improve the accuracy and efficiency of diagnosis.
Operation and Maintenance Management Recommendations
- Monitoring System: Establish a comprehensive monitoring system for multiple parameters such as temperature, sound, and oil quality to master the status in real - time.
- Environment Optimization: Optimize the installation position and method to reduce environmental impact.
- Pre - maintenance Tests: Regularly conduct preventive tests (insulation resistance tests, oil quality detection, etc.) to identify hidden dangers.
- Dynamic Adjustment: Adjust the operation mode and transformer capacity according to load changes.
- Technology Upgrade: Adopt high - efficiency and intelligent monitoring equipment to improve efficiency and diagnosis ability.
The development of the smart grid helps the fault diagnosis and management of single - phase distribution transformers to move towards intelligence and refinement. It is recommended that power companies introduce new technologies and standards, build a big data health management system, realize early fault warning and precise diagnosis, and improve the reliability and economy of the distribution network.