In the container structural scheme, the container is mainly constructed from steel plates, steel beams, steel columns, corner fittings, etc. The container structure is an integrated structure formed by combining steel plates and a frame. Based on the single - layer layout of the container, finite - element software is used to establish the container structure model, and then the building load of the container structure is simulated and calculated. The calculation results show that the stress generated in each component of the container is less than the allowable stress of the steel, and the deformation of the components is also less than the allowable value. It can be seen that the single - layer arranged container can well meet the structural load requirements of substation buildings.
The container - type frame structure adopts international general standards for both the overall structure and its components, which facilitates standardization. By leveraging the production capacity and equipment of existing container manufacturers in cooperation with secondary equipment manufacturers, mass production can be achieved through improvements, resulting in cost savings and good economic benefits. However, it is difficult to achieve an aesthetically pleasing appearance on the surface of the container. When used to build substations in areas with high environmental assessment requirements, such as urban areas and scenic spots, it often fails to pass the local environmental assessment review, posing significant obstacles to construction.
As a standard product, due to the limitations of its structural characteristics, the door - opening positions of the container are relatively fixed, and it is difficult to open doors at other positions, resulting in a lack of diversity in the scheme. In case of necessary door - opening, it will affect the stability and tightness of the container. Therefore, how to integrate the space required by electrical equipment into the pre - set fixed space is a major challenge in implementing the container structural scheme for substations.
Generally, the service life of transportation containers is 7 - 10 years. The designed service life of primary equipment in substations is 40 years, and that of secondary equipment is 20 years. If the container - type structure is adopted for substations, the durability of the container structure needs to be improved. The service life of the container structure is affected by many factors, such as the anti - corrosion coating scheme, the inherent durability of the materials, the equipment operating environment, and operation protection measures. After anti - corrosion treatment, if the container structure is placed in an area with a good environment, low dust and sand content, and minimal corrosiveness, its service life can reach 20 years or even 30 years. However, if placed in an area with a poor environment, its service life will be significantly reduced due to factors such as its own structural strength and the existing surface anti - corrosion processing technology.
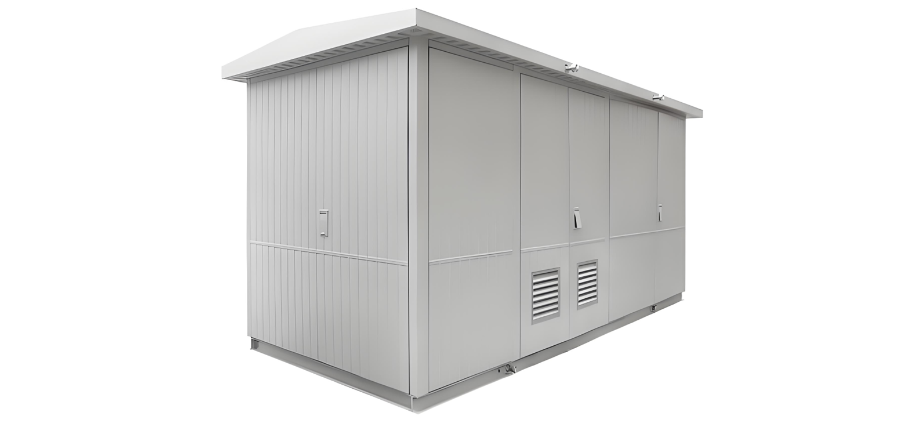
Jinbang plate is mainly made of cement, fly ash, silica powder, and perlite, reinforced with composite fibers. It is formed by vacuum high - pressure extrusion, cured under high - temperature and high - pressure steam, processed, and multi - layer sprayed. During the production process of Jinbang plate, no waste water, waste residue, or waste gas is generated, and it does not pollute the environment, making it a green and environmentally friendly building material product. The surface patterns of Jinbang plate can be combined with the surface coating process through mold design and development to achieve a variety of patterns and any combination of surface coating colors, creating a rich and colorful effect and making the surface of the equipment cabin visually appealing.
The Jinbang plate structure uses a skeleton composed of section steel as the basic load - bearing frame and adopts an external insulation method. The walls of the Jinbang plate structure are composed of materials such as Jinbang plate, ventilation layer, moisture - proof sealing film, oriented strand board, insulation materials, thin - walled square tubes, and gypsum board. The main raw materials for producing Jinbang plate are inorganic materials, endowing it with excellent fire - resistance. Whether used as curtain wall material or the surface layer of external wall insulation, Jinbang plate shows good fire - resistant performance.
At the same time, through mechanical calculations, the structure ensures the static and dynamic mechanical strength throughout the processes of hoisting, transportation, and installation, meeting the requirement of a 25 - year service life. It has the characteristics of high density, good weather resistance, stable dimensions, low deformation coefficient, water resistance, fire resistance, and resistance to weathering and freezing.Jinbang plate, similar to cement - based materials, has a good short - term appearance. However, its light and brittle nature, tendency to crack, and poor impact resistance significantly compromise the protective performance that the wall itself should possess. Jinbang plate is attached to the internal skeleton through hanging parts.
The joint parts of the plates are coated with elastic waterproof sealant. It adopts the methods of tongue - and - groove connection and fastener fixation, and special seam connectors are used at the plate joints, filled with elastic sealing materials. Due to the limitations of the material, the sealing performance at the door - plate connections is poor, which is not conducive to achieving dust - proof, moisture - proof, and anti - condensation effects. Slight deformation or vibration during transportation or hoisting can easily cause damage or cracking of the appearance, and in some cases, the Jinbang plate may even fall off.
Moreover, due to its poor mechanical properties, Jinbang plate can only be used independently as non - load - bearing exterior wall maintenance materials and building curtain wall materials, and cannot serve as a load - bearing structure, so it cannot provide support and strengthening functions. The existing process can only achieve the integration of single - layer equipment, and there is room for optimization in further three - dimensional structure integration.
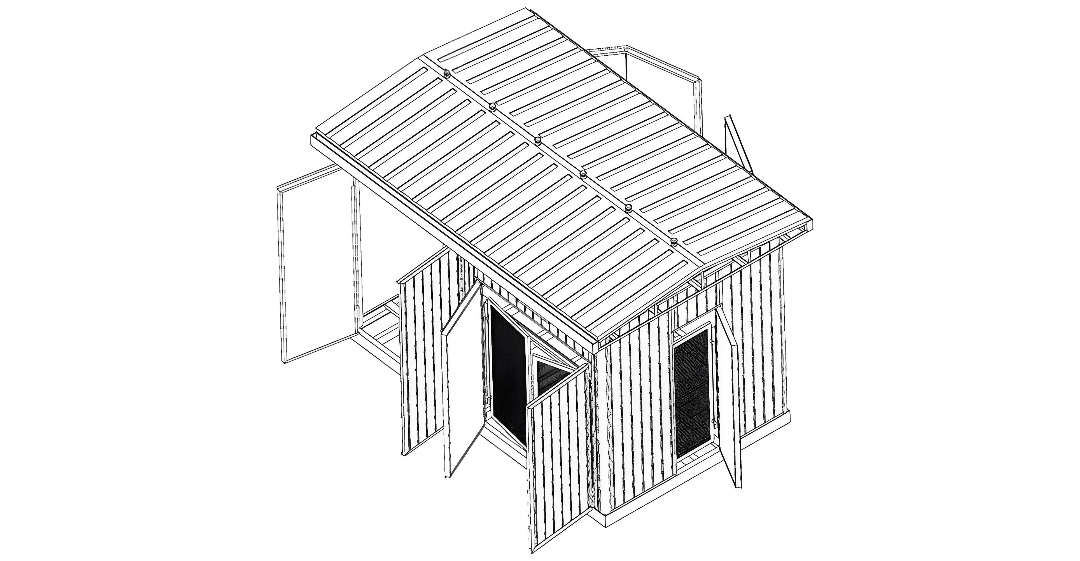
The structure of the prefabricated cabin is derived from mature design and manufacturing technologies of outdoor box - type substations, and it is a customized product specifically designed for the integrated installation of electrical equipment. The prefabricated cabin is a type of equipment with its own anti - deformation ability. The structural base is welded by section steel, and the cabin framework is an integrated welded structure. The main steel material used is high - quality carbon structural steel, which has sufficient mechanical strength, hardness, and yield strength, and exhibits strong environmental adaptability.
The exterior wall of the cabin is made of metal steel plates, which offer excellent decorative properties, providing various possibilities for exterior wall decoration. It can be flexibly spray - painted according to the on - site environment to perfectly blend with the surrounding environment and is more likely to be accepted by the local residents. When subjected to external forces during transportation, hoisting, etc., the cabin can undergo slight deformation to counteract the effects of these external forces and recover within a short period, protecting the installation of electrical components from mechanical forces, ensuring the dynamic stability of the electrical system, and effectively withstanding the impacts of external forces such as earthquakes.
In the structural design of the prefabricated cabin, a margin is reserved for the selection of steel materials and structures, which can effectively address the structural damage caused by earthquakes. The interior design of the prefabricated cabin is flexible. Section materials are used for reinforcement to increase the overall support strength, and a three - dimensional structural layout can be adopted. By applying this scheme, the occupied area is reduced, and the vertical space is utilized, achieving the conservation of land resources. Meanwhile, in the three - dimensional layout structure, vibration isolation devices are installed between the upper and lower layers to eliminate noise and reduce vibrations. The strength and seismic performance of the prefabricated cabin have been verified through finite - element analysis and by national authoritative testing institutions, ensuring sufficient reliability.
Both the framework and the top cover of the cabin are made of galvanized steel plates, and the wall panels are double - layer steel plates filled with fireproof, flame - retardant, and heat - insulating materials. Combined with the heat - insulation structure of the broken bridge, the heat conduction between the structures is reduced. When there is a fire inside or outside the cabin, the outer shell of the cabin can maintain its integrity and fire resistance within 3 hours, demonstrating excellent heat - insulation and fireproof performance.
The "car - like" sealing process is employed to achieve dust - proof, moisture - proof, and anti - condensation effects. Depending on the internal equipment and the application environment, the cabin structure, dimensions, maintenance doors, and cable entry/exit openings of the prefabricated cabin can be flexibly designed. According to the expansion requirements of the internal equipment, different equipment entry/exit openings can be reserved, and the top cover can be disassembled in sections, facilitating the installation of equipment in the later stage. This can meet different project requirements and offers a variety of design options.
The prefabricated cabin structure has good anti - corrosion performance. The anti - corrosion treatment adheres to the ISO12944 standard "Corrosion protection of steel structures by protective paint systems". Multiple anti - corrosion processes are adopted, including pretreatment, zinc layer, intermediate layer, surface layer, and other treatments, ensuring that the cabin can achieve an anti - corrosion level of no rusting within 30 years in a C4 environment. The operating life of the prefabricated cabin is designed to be more than 40 years, and with simple maintenance, it can reach a service life of 60 years.
Compared with the container structure, the prefabricated cabin structure has the following advantages: it can be flexibly designed according to actual needs, has a larger internal space, provides better operation and maintenance conditions, and is less affected by road transportation conditions.
With the proposal of the concept of a green power grid, green construction concepts such as intelligence, high efficiency, reliability, economic practicality, optimal benefits over the entire life cycle, land conservation, energy conservation, water conservation, material conservation, and environmental protection have been put forward for substation construction. Prefabricated substations, which use prefabricated equipment, are in line with the concept of a green power grid and are characterized by fast construction speed, small footprint, high system integration, convenient transportation, and quick installation.
Compared with the container structure and the Jinbang plate structure, the prefabricated cabin structure exhibits more characteristics and advantages. The structural mode of the prefabricated cabin has outstanding advantages such as safety and reliability, strong environmental adaptability, flexible layout, high operability in operation, maintenance, and inspection, as well as energy conservation and environmental protection. It has demonstrated great advantages in practical applications and holds extensive application value.