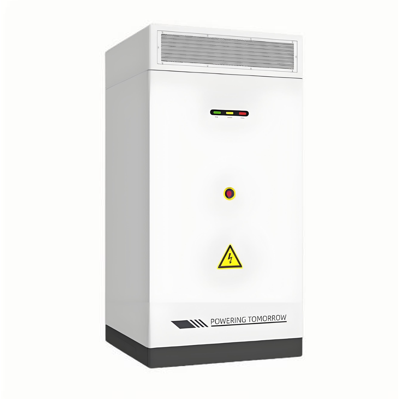
Ⅰ. Energy Pain Points and Retrofitting Needs in Aging Industrial Parks
- High Electricity Costs
- Significant peak-valley price disparity (e.g., peak: ¥1.2/kWh vs. valley: ¥0.3/kWh), with peak-hour consumption accounting for over 40% of total costs.
- Insufficient transformer capacity, coupled with prohibitively high expansion costs (over ¥500,000 per unit upgrade).
- Spatial and Equipment Limitations
- Compact layout leaves no reserved space for energy storage, making traditional containerized energy storage systems unfeasible.
- Aging equipment with low efficiency and lack of real-time monitoring, resulting in 20%-30% higher energy intensity than advanced factories.
- Poor Power Supply Stability
- Unexpected blackouts cause production interruptions, incurring annual losses exceeding millions; inadequate backup energy storage capacity.
- Carbon Pressure and Policy Drivers
- High reliance on traditional energy sources triggers surging carbon tax costs (e.g., annual emissions >1,500 tons risk million-level fines).
- Government subsidies (e.g., ¥0.5/kWh for energy storage) incentivize upgrades.
II. ICESS Core Solutions
- Modular Energy Storage System: Overcoming Spatial Constraints
- Ultra-slim design: ≤90cm-wide modular units (e.g., SigenStack) embed into building gaps/equipment interlayers without foundation modifications.
- Distributed load-bearing: Single-unit weight <300kg; two-person installation adapts to structural limits of aging plants.
- Scalable capacity: From 100kW/200kWh to 10MW+ (supporting Li-ion, flow batteries, etc.).
- Integrated PV-Storage-Charging: Dynamic Energy Optimization
Component
|
Solution
|
Benefits
|
PV Generation
|
Mono-crystalline panels (≥22% efficiency) on roofs/carports; AI-powered yield forecasting; anti-reverse protection to avoid grid penalties.
|
Annual output: 2.4M kWh (2MW system), covering 30% of daytime load.
|
Smart Storage
|
Valley-charging & peak-discharging (price arbitrage); demand management to flatten load curves (30% peak-load reduction on transformers).
|
30% higher ROI per cycle; payback period <4 years.
|
Charging Piles
|
7-240kW full coverage; time-of-use pricing + sequential charging (prevents transformer overload).
|
60% lower charging cost for forklifts; 40% reduction for employee vehicles.
|
3.Multi-Timescale Energy Storage Configuration
Storage Type
|
Response Time
|
Application Scenario
|
Aging Plant Case
|
Supercapacitors
|
<1 second
|
Voltage sag support; elevator regenerative absorption.
|
Ensures uninterrupted precision instrument production.
|
Li-ion Storage
|
Minutes
|
Daily peak shaving (2-4h discharge).
|
Replaces diesel generators for 2h emergency backup.
|
LH₂/Compressed Air
|
Hours+
|
Weekly/monthly regulation; winter heating.
|
Repurposes abandoned pipelines for energy storage (Xiaoshan case).
|
III. AI-Driven Smart Management Platform
- Real-time monitoring: Integrates PV, storage, and charging pile data for dynamic "source-grid-load-storage" visualization.
- AI-powered scheduling: Prioritizes green energy consumption; automatically dispatches storage/grid power during shortages; adjusts non-urgent production lines/charging pile load.
- Carbon management: Auto-generates emission reports aligned with industry standards; supports carbon credit trading.
- Smart O&M: Proactive fault alerts (>95% accuracy); automated work orders; 50% higher maintenance efficiency.
IV. Retrofitting Implementation Roadmap
- Spatial Assessment & Design
- Use BIM scans to identify idle space (e.g., gaps ≥90cm can deploy 1MWh systems).
- Phased Deployment
- Phase 1: Modular storage + smart charging piles (commissioned in 3 months for basic peak-shaving).
- Phase 2: Expand rooftop PV + long-duration storage (e.g., retrofit abandoned hydrogen tanks for LH₂ storage).
- Policy & Funding Coordination
- Secure local subsidies and green loans.
V. Benefit Analysis
Metric
|
Pre-retrofit
|
Post-retrofit
|
Improvement
|
Annual Electricity Cost
|
¥24 million
|
¥19 million
|
↓20.8%
|
Transformer Expansion Need
|
30% capacity increase
|
Zero new capacity
|
Saves ¥3 million
|
Power Supply Reliability
|
20 hours downtime/yr
|
<2 hours downtime/yr
|
↑90%
|
Carbon Reduction
|
1,500 tons/yr
|
Certified Zero-Carbon Park
|
Provincial Green Factory Award
|
VI. Case Study: Mannheim Energy Hub Transformation
Pain Point: An 8-hectare retired coal plant site with dense underground pipelines; zero available land for new large-scale storage.
Solution:
- Maximized existing infrastructure: Integrated original grid access points to deploy 50MW/100MWh LFP storage (zero new land use).
- Space-optimized embedding: 30 ISO-standardized containerized units retrofitted into abandoned plant structures.
Benefits:
- Scalability & Capacity: Annual peak-shaving = 200% of local peak load; 100MWh storage powers critical industries >2 hours.
- Environmental & Economic Returns:
- Annual CO₂ reduction: 7,500 tons (equivalent to 3M liters of fuel saved or 85+ hectares reforested).
- Annual revenue >€1.5M via electricity arbitrage & grid frequency regulation services.