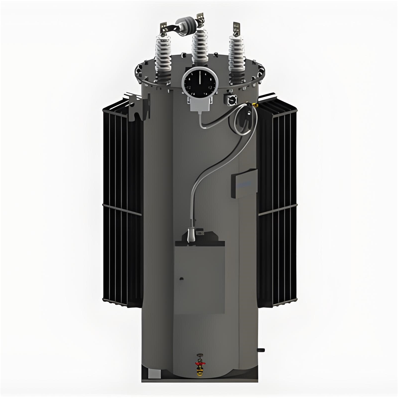
1. Working Principle and Technological Evolution of Step Voltage Regulators
The Step Voltage Regulator (SVR) is a core device for voltage regulation in modern substations, achieving precise voltage stabilization through tap-changing mechanisms. Its core principle relies on transformer ratio adjustment: when voltage deviation is detected, a motor-driven system switches taps to alter the winding turns ratio, adjusting the output voltage. Typical SVRs provide ±10% voltage regulation with step increments of 0.625% or 1.25%, complying with the ANSI C84.1 standard for voltage fluctuations.
1.1 Stepwise Regulation Mechanism
- Tap Switching System: Combines motor-driven mechanical switches and solid-state electronic switches. Utilizes a "make-before-break" principle with transition resistors to limit circulating current, ensuring uninterrupted power supply. Switching completes within 15–30 ms, preventing voltage sags for sensitive equipment.
- Microprocessor Control Unit: Equipped with 32-bit RISC processors for real-time voltage sampling (≥100 samples/sec). Employs DSP-based FFT analysis to separate fundamental and harmonic components, achieving measurement accuracy of ±0.5%.
1.2 Modern Digital Control Technologies
Integrated multifunctional control modules enable complex scenario optimization:
- Automatic Voltage Reduction (VFR): Reduces output voltage during system overload, lowering losses by 4–8%. Formula: Eff. VSET = VSET × (1 - %R), where %R (typically 2–8%) defines the reduction ratio. For example, a 122V system with 4.9% reduction outputs 116V.
- Voltage Limiting: Sets operational bounds (e.g., ±5% Un). Automatically intervenes during voltage violations, overrideable by local/remote operators or SCADA.
- Fault Ride-Through: Maintains basic regulation during faults (e.g., voltage drops to 70% Un). EEPROM storage preserves critical parameters for ≥72 hours post-outage.
2. Substation System Integration Solutions
2.1 Transformer Tap Control & Parallel Compensation
Voltage regulation requires coordinated control of multiple devices:
- On-Load Tap Changer (OLTC): Primary regulator with ±10% range. Modern OLTCs use electronic position sensors (±0.5% accuracy) to transmit real-time data to SCADA.
- Capacitor Banks: Automatically switched based on reactive power demand. Typical configurations: 4–8 groups, capacity at 5–15% of transformer rating (e.g., 2–6 Mvar for 33kV systems). Control strategies must balance voltage deviation and power factor (target: 0.95–1.0) to avoid overcompensation.
2.2 Line Drop Compensation Technologies
Long-distance feeders use distributed regulation strategies:
- Series Compensation: Install series capacitors on 10–33kV overhead lines to compensate 40–70% of line reactance. Example: A 2000μF capacitor at 15 km mid-point boosts end voltage by 4–8%, protected by MOV surge arresters.
- Line Voltage Regulators (SVRs): Deployed 5–8 km from substations. Capacity: 500–1500 kVA, range ±10%. Integrated with Feeder Terminal Units (FTUs) for localized automation, reducing communication dependency.
2.3 Equipment Configuration
Device Type
|
Function
|
Key Parameters
|
Typical Location
|
OLTC Transformer
|
Primary voltage control
|
±8 taps, 1.25%/step, <30s response
|
Substation main transformer
|
Capacitor Banks
|
Reactive compensation
|
5–15 Mvar, <60s switching delay
|
35kV/10kV bus
|
Line Regulator (SVR)
|
Mid-voltage compensation
|
±10 taps, 0.625%/step, 500–1500kVA
|
Feeder midpoint
|
SVG
|
Dynamic compensation
|
±2 Mvar, <10ms response
|
Renewable grid connection
|
3. Advanced Control Strategies
3.1 Traditional Nine-Zone Control & Improvements
The voltage-reactive power plane is divided into 9 zones to trigger predefined actions:
- Zone Logic: Boundaries set by voltage limits (e.g., ±3% Un) and reactive limits (e.g., ±10% Qn). Example: Zone 1 (low voltage) triggers voltage increase.
- Limitations: Boundary oscillations cause frequent device actions (e.g., capacitor switching in Zone 5), and fail to handle multi-constraint coupling (e.g., voltage violation + reactive deficiency).
3.2 Fuzzy Control & Dynamic Zoning
Modern systems adopt fuzzy logic to overcome limitations:
- Fuzzification: Defines voltage deviation (ΔU) and reactive deviation (ΔQ) as fuzzy variables (e.g., Negative Large to Positive Large), with trapezoidal membership functions.
- Rule Base: 81 fuzzy rules enable nonlinear mapping, e.g.:
- IF ΔU is Negative Large AND ΔQ is Zero THEN Raise Voltage.
- Dynamic Adjustment: Expands voltage dead zones during heavy loads (±1.5%→±3%), reducing device actions by 40–60%.
3.3 Multi-Objective Optimization
For distributed energy integration scenarios:
- Objective Function:
Min[Ploss + λ1·(Uref - Umeas)² + λ2·(Qbalance) + λ3·(Tap_change)]
(λ: weighting coefficients; Tap_change: tap operation cost)
- Constraints:
- Voltage safety: Umin ≤ Ui ≤ Umax
- Device capacity: |Qc| ≤ Qcmax
- Daily tap operations: ∑|Tap_change| ≤ 8
- Algorithm: Improved PSO optimization with 50 particles converges in <3s, meeting real-time requirements.
4. Communication & Automation Support Systems
4.1 IEC 61850 Communication Architecture
- GOOSE Messaging: Supports inter-station commands with <10ms delay. Enables coordinated voltage control (e.g., sub-stations respond within 100ms to main-station commands).
- Information Modeling: Defines logical nodes (e.g., ATCC for tap control, CPOW for capacitors), each with 30+ data objects (e.g., TapPos, VoltMag) for plug-and-play integration.
4.2 SCADA System Integration
- Data Acquisition: RTUs sample critical data (voltage, current, tap position) every 2 seconds, prioritizing voltage data transmission.
- Control Functions:
- Remote parameter adjustment (e.g., VSET, %R).
- Seamless auto/manual mode switching.
- Automatic operation lock during device faults.
- Visualization: Dynamic single-line diagrams (voltage violations highlighted in red), trend curves, and audible alarms.
4.3 Key Communication Protocols
Layer
|
Technology
|
Performance
|
Application
|
Station Level
|
MMS
|
Delay <500ms
|
Monitoring data upload
|
Process Level
|
GOOSE
|
Delay <10ms
|
Protection & control
|
Inter-Station
|
R-GOOSE
|
Delay <100ms
|
Multi-station coordination
|
Security Layer
|
IEC 62351-6
|
AES-128 encryption
|
All communication layers
|
5. Performance Optimization & Validation
5.1 Voltage Optimization (VO) Protocol Implementation
U.S. Energy Association’s three-tier approach:
- Fixed Voltage Reduction (VFR): Full-time 2–3% reduction (e.g., 122V→119V). Suitable for stable loads. Annual savings: 1.5–2.5%, but risks motor startup issues.
- Line Drop Compensation (LDC): Dynamically adjusts voltage based on load current.
- Automatic Voltage Feedback (AVFC): Closed-loop control using 3–5 remote sensors/feeder. PID algorithm with 30s cycles.
5.2 Performance Quantification
- Data Collection: 0.2S-class power analyzers record voltage, THD, and power parameters (1s intervals, 7-day duration).
- Energy Savings Calculation: Regression analysis excludes temperature effects.
- Key Metrics:
- Voltage compliance rate: >99.5%
- Daily device actions: <4
- Line loss reduction: 3–8%
- Capacitor switching lifespan: >100,000 cycles.
5.3 Optimization Technique Comparison
Technique
|
Cost
|
Energy Savings
|
Voltage Improvement
|
Applicability
|
VFR
|
Low
|
1.5–2.5%
|
Limited
|
Stable load areas
|
LDC
|
Medium
|
2–4%
|
Significant
|
Long feeders
|
AVFC
|
High
|
3–8%
|
Excellent
|
High-demand zones
|
Fuzzy Control
|
High
|
5–10%
|
Optimal
|
High renewable penetration
|