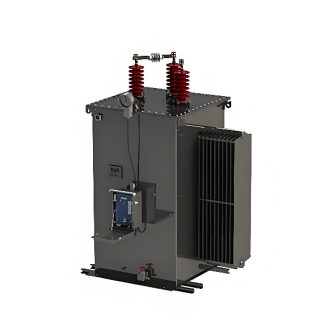
1 Executive Summary
Voltage Management Challenges in Modern Distribution Networks:
- Long-distance feeders causing voltage drop;
- Distributed energy resource (DER) integration leading to bidirectional power flow;
- Load fluctuations causing frequent voltage variations.
Technical Features of Step Voltage Regulators (SVRs):
- Employs tap-changing technology to alter transformer winding turns ratio, achieving a ±10% voltage adjustment range (typically in 32 steps, 0.625% per step);
- Core advantages lie in real-time dynamic adjustment capabilities combined with multiple control strategies, providing flexible voltage support for the distribution grid.
Technology Evolution Trends:
- Evolved from basic mechanical tap switches to integrated systems incorporating power electronics, adaptive control algorithms, and intelligent communication modules;
- Representative example: The ABB SPAU341C integrates Line Drop Compensation (LDC) functionality, simulating line impedance characteristics for precise voltage control at remote load points;
- Utilization of magnetically held relays and TRIACs reduces equipment losses and footprint, enhancing deployment flexibility and cost-effectiveness.
2 Technical Principle & Structure
Core Voltage Regulation Mechanism:
- Achieves voltage regulation by changing the transformer winding turns ratio, relying on the tap-changing technology of On-Load Tap Changers (OLTCs).
Closed-Loop Feedback Control Process:
- Voltage transformers continuously acquire system voltage signals;
- Error signals are generated by comparing acquired values with set reference values;
- The control unit decides tap change direction (boost/buck) and step size based on the error signal.
Key Technical Parameters of Modern SVRs:
- Taking the SPAU341C as an example: Supports fine voltage adjustment steps of 0.625%, enabling 32-step precise voltage regulation within a ±10% range.
2.1 Core Components
- On-Load Tap Changer (OLTC): The core actuator of the regulator, utilizing vacuum interrupters to reduce arcing. Transition resistors ensure current continuity during switching, preventing load supply interruption. Modern designs employ dual-resistor transition technology, reducing switching times to 40-60 milliseconds.
- Control Module: Built on high-performance microprocessors (ARM/DSP), integrating multiple control strategies. The ABB SPAU341C adopts a modular architecture, comprising connection modules, I/O modules, and an automatic voltage regulation module, supporting continuous self-monitoring for real-time hardware and software diagnostics.
- Measurement and Protection Unit: Voltage/Current Transformers (e.g., PT1, PT2, TA1) continuously gather system parameters. Units are equipped with three-phase overcurrent and undervoltage blocking functions. Upon detecting a short circuit or severe voltage dip, tap-changing operations are immediately blocked to prevent equipment damage.
- Communication and Operation Interface: Supports Ethernet, GPRS, and other communication protocols for remote monitoring and parameter settings. The display module provides a local operating interface, showing key parameters like setpoints and measured values in real-time.
2.2 Key Operational Characteristics
Characteristic
|
Technical Description
|
Application Value
|
Line Drop Compensation (LDC)
|
Uses virtual impedance parameters (R/X) settings to compensate for line voltage drop.
|
Enables precise voltage control at remote load points; eliminates need for additional measurement devices.
|
Bidirectional Power Flow Support
|
Employs hybrid switches combining back-to-back thyristors and magnetic latching relays.
|
Adapts to scenarios with DER integration; supports voltage regulation under reverse power flow.
|
Parallel Operation Capability
|
Supports parallel operation of up to 3 transformers via Master/Slave or Circulating Current Minimization principles.
|
Expands system capacity; meets demands of high-load density areas.
|
Fault Ride-Through (FRT) Capability
|
Incorporates voltage sag detection and fast restoration logic.
|
Ensures continuous supply for sensitive loads; enhances power supply reliability.
|
3 Application Solutions in Distribution System Design
3.1 Typical Application Scenarios
- Long Radial Feeders: A classic SVR application. In rural distribution networks, 10kV lines often extend over 15km, causing severe voltage deviation at the feeder end. Deploying SVRs mid-line or at the feeder end effectively compensates for voltage drops. Engineering practices show that a single SVR can extend the feeder radius by 30%, improving the voltage compliance rate at the feeder end from below 70% to over 98%, significantly reducing line upgrade costs.
- High-Density Urban Distribution Networks: Face challenges of load fluctuation and voltage mismatch. SVRs are typically installed at substation outlets or ring main unit (RMU) nodes. In a city commercial district retrofit project, installing SVRs at 4 key nodes reduced peak-hour voltage fluctuation from ±8% to ±2%, while simultaneously reducing line losses by 12% through reactive power optimization.
- High DER Penetration Areas: Require managing bidirectional power flow challenges. When PV penetration exceeds 30%, traditional distribution networks often experience voltage violations. SVRs automatically adjust control logic via a reverse power mode, actively reducing voltage during periods of generation surplus. A PV demonstration project using coordinated control between SVRs and PV inverters increased local PV hosting capacity by 25% and reduced curtailment rates by 18%.
3.2 Control Strategy Optimization
- Voltage-Var Optimization (VVO): Coordinates SVRs with shunt capacitor banks to minimize system losses.
- Multi-Stage Coordinated Control: For cascade installations of multiple SVRs in complex networks, control conflicts must be avoided. The Time Delay Coordination Method is the most practical solution—setting the upstream SVR's delay (typically 30-60 seconds) to at least double the downstream SVR's delay. Upon detecting a voltage violation, the downstream SVR acts first. If the issue persists beyond its delay window, the upstream SVR then intervenes. This approach significantly reduces unnecessary tap operations (by up to 40%) while maintaining voltage stability.
- Adaptive Control Strategies: Modern SVRs (e.g., SPAU341C) incorporate self-learning algorithms to predict voltage adjustment needs based on historical load profiles. The system automatically pre-adjusts tap positions during periods of similar daily load patterns (e.g., morning peaks), reducing voltage adjustment response times from minutes to seconds. This strategy is particularly suitable for PV output fluctuations or scenarios with concentrated electric vehicle (EV) charging.
3.3 Scenario Selection Matrix
Application Scenario
|
Equipment Selection Criteria
|
Control Strategy
|
Expected Outcome
|
Long Radial Feeders
|
Large adjustment range (±15%), strong heat dissipation
|
LDC + Delayed Coordination
|
End voltage boost: 8-12%, Feeder radius extension: 30%
|
High-Density Urban Areas
|
Fast response (<1s), compact design
|
VVO Coordination + Load Forecasting
|
Voltage fluctuation <±2%, Network losses reduction: 10-15%
|
High DER Penetration Areas
|
Bidirectional flow support, high overload capability
|
Reverse Power Mode + Source-Grid Coordination
|
PV hosting capacity ↑25%, Voltage compliance rate >99%
|
4 Performance Optimization & Innovative Technologies
Loss Reduction Technology:
Hybrid switching technology is a core innovation for minimizing SVR losses. Traditional mechanical tap changers suffer from contact resistance in the tens of mΩ and significant arcing losses. The modern solution employs a hybrid structure of Magnetic Latching Relays and Back-to-Back Thyristors:
- Steady-State Conduction: Handled by the Magnetic Latching Relay (contact resistance <1mΩ)
- Transition Moment: The Back-to-Back Thyristor provides a current path (trigger time <2μs)
- Post-Switch Steady-State: Mechanical contacts close again, semiconductor devices turn off.
This design reduces switching losses by 80%, shrinks equipment volume by 40%, achieves arc-less switching, and extends equipment lifespan. Actual operating data shows hybrid-switch SVRs incur 55% lower annual maintenance costs compared to traditional models.
Topology Innovation also contributes significantly. The Cascaded Voltage Regulator adopts a hybrid structure with a series transformer and shunt capacitor, offering three optional operating modes:
- Equivalent Series Compensation Mode: Targets voltage boost at the end of long lines.
- Voltage-Var Adjustment Mode: Coordinates voltage and reactive power optimization.
- Pure Voltage Regulation Mode: Enables rapid response to voltage sags.
This design reduces system losses by 15-20% at the same capacity while improving fault ride-through capability.
5 Application Cases & Practical Experience
5.1 Voltage Boost on Rural Long-Distance Feeder
- Project Background: A 28km 10kV feeder in a mountainous area supplied dispersed loads. End voltage during peak hours dropped to 8.7kV (below standard lower limit: 9.7kV), failing to meet power requirements for irrigation pumps. Traditional solutions required a new substation at over ¥8 million cost.
- Solution: Two ABB SPAU341C regulators deployed in series at the 12km and 22km points, utilizing a Master-Slave coordination strategy.
- Device Configuration: Each SVR: 800kVA, ±15% range, LDC-enabled.
- Control Strategy: Master station (22km) delay: 60 seconds; Slave station (12km) delay: 30 seconds.
- Compensation Parameters: Virtual R = 0.32Ω, X = 0.45Ω (simulating line impedance).
- Results:
- End voltage stabilized at 9.8-10.2kV; compliance rate rose from 61% to 99.6%.
- Insufficient starting torque issue for pumps during irrigation season peak load completely eliminated.
- Total investment: ¥1.8 million (77.5% cost reduction vs. new substation).
- Annual energy loss reduction: ~150 MWh, corresponding to energy cost savings of ~¥120,000.
5.2 Power Quality Improvement in Urban High-Density Area
- Project Background: Within an urban RMU's supply area, clustered commercial complexes and EV charging stations caused voltage fluctuations reaching ±8%. Transformer loading reached 130% during peak hours.
- Solution: Deployment of an SVR + Dynamic Var Compensation (SVG) system at the RMU inlet.
- Device Selection: SPAU341C Regulator (1250kVA) with ±200kVar SVG.
- Control Architecture: VVO coordination controller performing joint optimization every 5 minutes.
- Prediction Algorithm: Deep learning-based load forecasting (accuracy >92%).
- Results:
- Voltage fluctuation controlled within ±2% (compliant with IEEE 519).
- Transformer loading reduced to 85%, freeing up 30% capacity.
- Comprehensive line losses reduced from 7.8% to 6.2%, yielding annual savings ~¥80,000.
- Charging pile failure rate reduced by 40%; user complaints decreased by 90%.