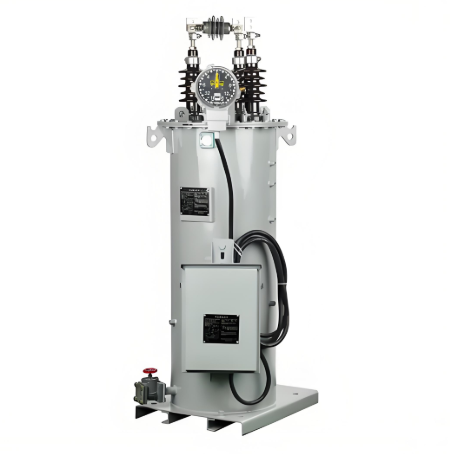
Ⅰ. Working Principle of 32-Step Voltage Regulator
(I) Basic Concepts and Control Principles
- Core Function: Based on discrete control principles, it achieves output voltage regulation through precise voltage gradations.
- Control Strategy Difference: Unlike traditional continuous-feedback regulators, it uses 32 fixed voltage levels for accurate adjustments, enabling rapid switching to preset levels.
(II) Structural Implementation and Case Studies
- Mechanical Solution
- Principle: Utilizes an autotransformer with 32 tap switches to change winding ratios, enabling stepwise voltage adjustment.
- Application Case: In 10kV distribution networks, each tap step adjusts voltage by 10% of the line voltage.
- Digital Solution
- Principle: Employs switching circuits and microcontrollers (e.g., STM32) to control resistor networks or inductors for discrete voltage steps.
- Application Case: A converter-based design uses 9 resistors + 8 switches to achieve 0.2V/step adjustment (output range: 0.1–32V).
(III) Technical Advantages and Performance
- Voltage Resolution:
- Autotransformer: Broad adjustment range per step but finer control with 32 levels.
- Digital Control: Achieves steps as low as 0.1V using precise resistor-switch combinations.
- Dynamic Response: Discrete control enables faster response (1–10 ms), meeting rapid voltage stabilization needs.
II. Technical Features of 32-Step Voltage Regulator
- High-Precision Control
- Core Advantage: 32-step gradation enables minimal step values (e.g., 0.2V/step), surpassing traditional linear regulators.
- Implementation: Digital potentiometers, MOSFET arrays, and microcontrollers ensure accuracy.
- Applications: Medical devices, semiconductor manufacturing, and precision instruments.
- Rapid Dynamic Response
- Response Time: 1–10 ms for level switching, outperforming traditional regulators limited by loop bandwidth.
- Value: Quickly stabilizes voltage during load/input fluctuations, ensuring system stability.
- Wide-Range Regulation
- Range: Supports 0–520V in three-phase systems, with customizable input voltage.
- Scenarios: Renewable energy integration, industrial automation, and power grid management.
- Comprehensive Protection
- Mechanisms: Integrated overcurrent/voltage/temperature protection and short-circuit safeguards.
- Case: Synchronous rectification circuits reduce losses while enhancing safety.
- Cost Efficiency
- Mechanical: Low-cost structure with minimal maintenance.
- Digital: Microcontrollers (e.g., TMC-series chips) reduce system complexity.
III. Performance Comparison: 32-Step vs. Traditional Regulators
Performance Metric
|
32-Step Regulator
|
Traditional Regulator
|
Regulation Accuracy
|
32 steps; ≤0.2V/step
|
Limited by noise/loop delay
|
Dynamic Response
|
1–10 ms
|
µs-range but bandwidth-constrained
|
Efficiency
|
Mechanical: ~70%; Digital: 85–90%
|
Linear: Low (e.g., 38%); Switching: 90%+
|
Cost
|
Mechanical: Low; Digital: Moderate
|
Linear: Low; Switching: High
|
IV. Application Scenarios
- Medical Equipment
- Use: Powers MRI/CT scanners, ensuring imaging precision and safety.
- Value: Matches demands for stable output and fast response.
- Semiconductor Manufacturing
- Core Role: Controls lithography laser sources (e.g., 0.625% voltage/step), critical for chip yield.
- Renewable Energy Integration
- Solution: Combines with SVC/SVG devices for grid voltage stabilization, handling renewable output fluctuations.
- Industrial Automation
- Implementation: Drives servo systems in CNC machines/robots, enhancing machining accuracy.
- Communication Equipment
- Benefit: Reduces power noise in base stations via precise voltage control.
V. Technical Implementation Schemes
- Mechanical Autotransformer
- Principle: 32 physical taps adjust winding ratios.
- Pros/Cons: Simple/low-cost but prone to contact wear.
- Use Case: Cost-sensitive, wide-range scenarios (e.g., power grids).
- Digital Switching Circuit
- Design: MOSFET arrays + microcontroller (e.g., STM32) for 0.1V/step resolution.
- Advantage: High precision, fast response, low maintenance.
- Applications: Precision instruments and test equipment.
- Hybrid Solution
- Structure: Autotransformer + electronic relays + digital control (e.g., 0.5V/step).
- Balance: Cost-effectiveness with enhanced flexibility.
- Microcontroller Functions
- Roles: Generates step signals, manages switches, and enables protection logic (e.g., overcurrent/temperature).
- Protection Mechanisms
- Features: Real-time monitoring for overcurrent/voltage/temperature, with shutdown triggers.
- Value: Ensures reliability in critical systems like industrial automation.