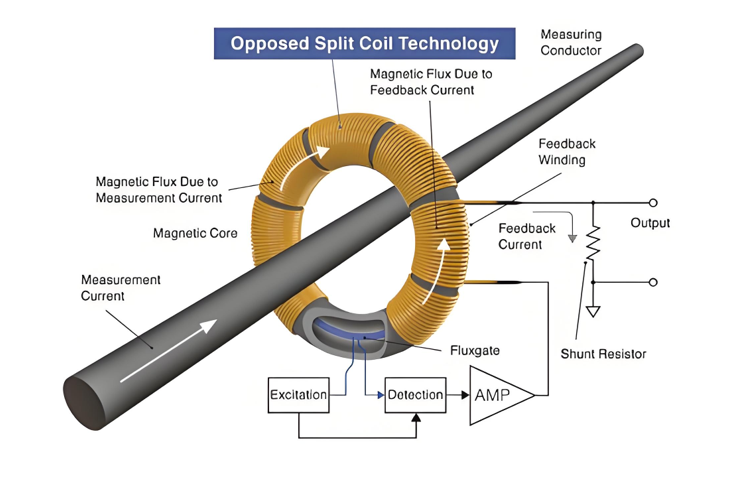
The increasing complexity of the power grid, especially with the incorporation of power - electronic - based devices, necessitates traceable measurement techniques. These are crucial for accurately ascertaining the high - frequency components of high electrical currents. In the non - intrusive measurement of both AC and DC electrical currents, magnetic coupling in current transformers is extensively employed.
The error of a current transformer is directly related to the magnetization of its core. This inherent connection naturally prompts the exploration of methods to mitigate this magnetic flux. One such approach is the zero - flux technique. In this technique, a balancing compensating current is introduced to induce zero - flux within the magnetic core.
Zero - flux current transformers belong to the category of Low - Power Instrument Transformers (LPITs). LPITs offer numerous advantages, including smaller size, lower power consumption, enhanced safety, higher accuracy, and improved signal reliability. With the implementation of digital communication in substations in accordance with the IEC61850 - 9 - 2 standard, the utilization of LPITs in Gas - Insulated Substations (GIS) is set to become more prevalent.
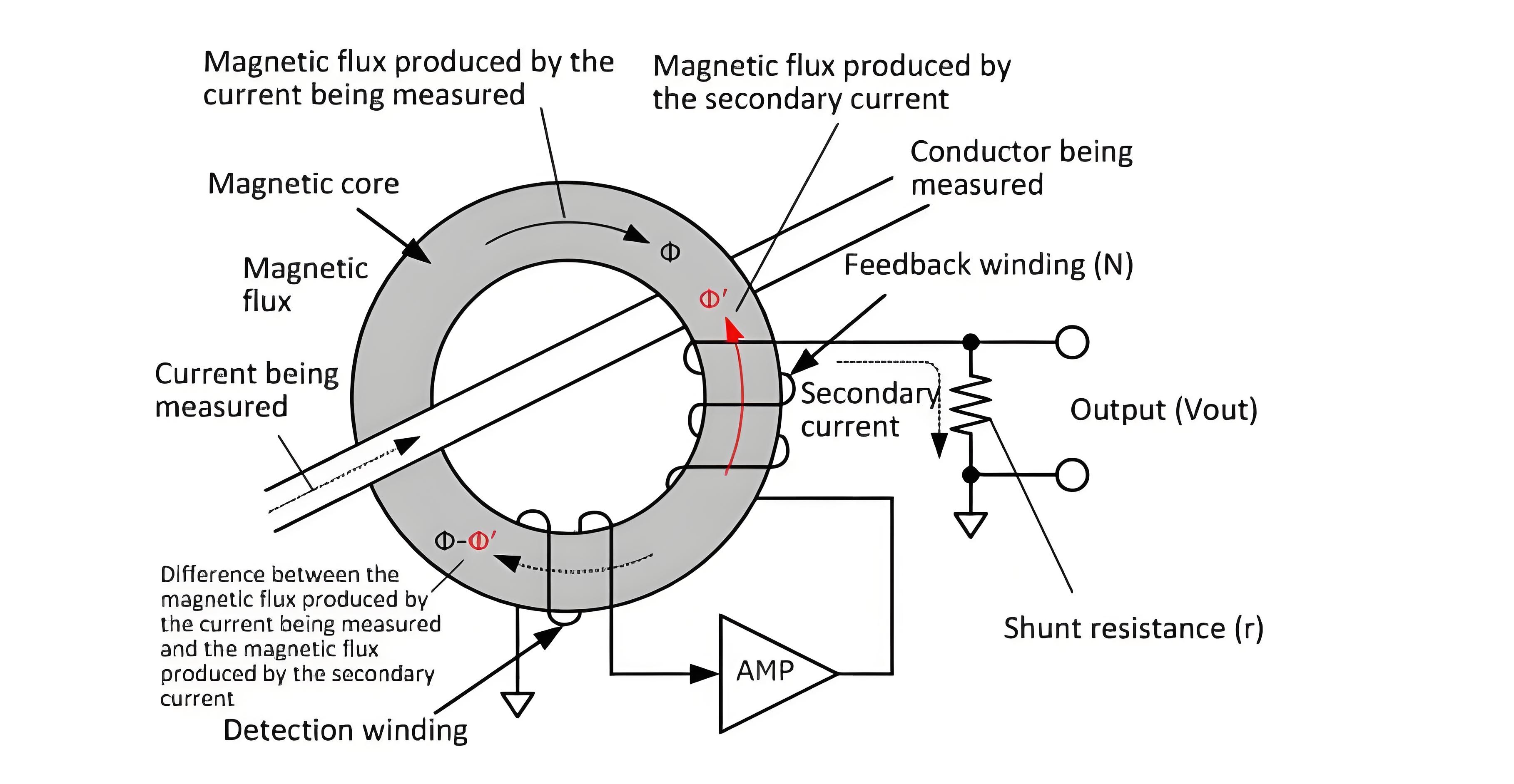
A detection winding is responsible for sensing the magnetic flux within the core. A closed - loop control system, consisting of an amplifier and a feedback winding, generates a secondary current. This secondary current is designed to counteract the flux produced by the primary current, thereby creating a “Zero - flux CT”. The secondary current then passes through a precision burden resistor, generating a voltage signal that is proportional to the primary current. In this setup, the magnetic material of the core remains unexcited, ensuring that it does not exhibit hysteresis or saturation effects.However, at DC or low - frequency conditions, the flux cancellation mechanism faces challenges. The detection winding is incapable of measuring the residual flux under such circumstances, and thus, the flux cannot be effectively canceled. To address DC measurements, a DC flux sensor is incorporated. This can be either a Hall probe embedded within the core or a flux - gate circuit equipped with two additional control and sensing windings.Advantages of Zero - flux Current TransformersAC zero - flux sensors exhibit high linearity and precision. They are immune to the characteristics of the magnetic core, resulting in a small phase error. The accuracy of these sensors is primarily determined by the precision of the burden resistor.The addition of a Hall probe or a flux - gate detector enables the measurement of DC currents.These sensors are highly resistant to electromagnetic interference, ensuring reliable operation in various electromagnetic environments.Disadvantages of Zero - flux Current TransformersThe sensor requires an external power supply and an amplifier to function.A malfunctioning secondary circuit has the potential to generate hazardous voltages, posing a safety risk.Example of Zero - flux Current Transformer Usage in the Kii - Channel Project HVDC Link for Outdoor 500 kV DC GISIn the Kii - Channel project, zero - flux CTs are utilized. Figure 2 presents the block diagram and the hardware details of the CT. The current to be measured, (Ip), generates a magnetic flux which is influenced by the current (Is) in the secondary winding ((Ns)).Three toroidal cores, located within the GIS compartment, are employed to sense the flux. Cores (N1) and (N2) are dedicated to sensing the DC components of the remaining flux, while (N3) is responsible for detecting the AC component. An oscillator drives the pair of DC - flux - sensing cores ((N1) and (N2)) into saturation in opposite directions. If the remaining DC flux is zero, the resulting current peaks in both directions will be equal. However, if the DC flux is non - zero, the difference between these peaks is proportional to the residual DC flux. By combining the AC component detected by (N3), a control loop is established. This loop generates the secondary current (Is) in such a way that it nullifies the overall flux. A power amplifier supplies the current (Is) to the secondary winding (Ns). Subsequently, the secondary current is directed to the burden resistor, which converts the current into an equivalent voltage signal. The measurement precision is determined by both the burden resistor and the stability of the differential amplifier.
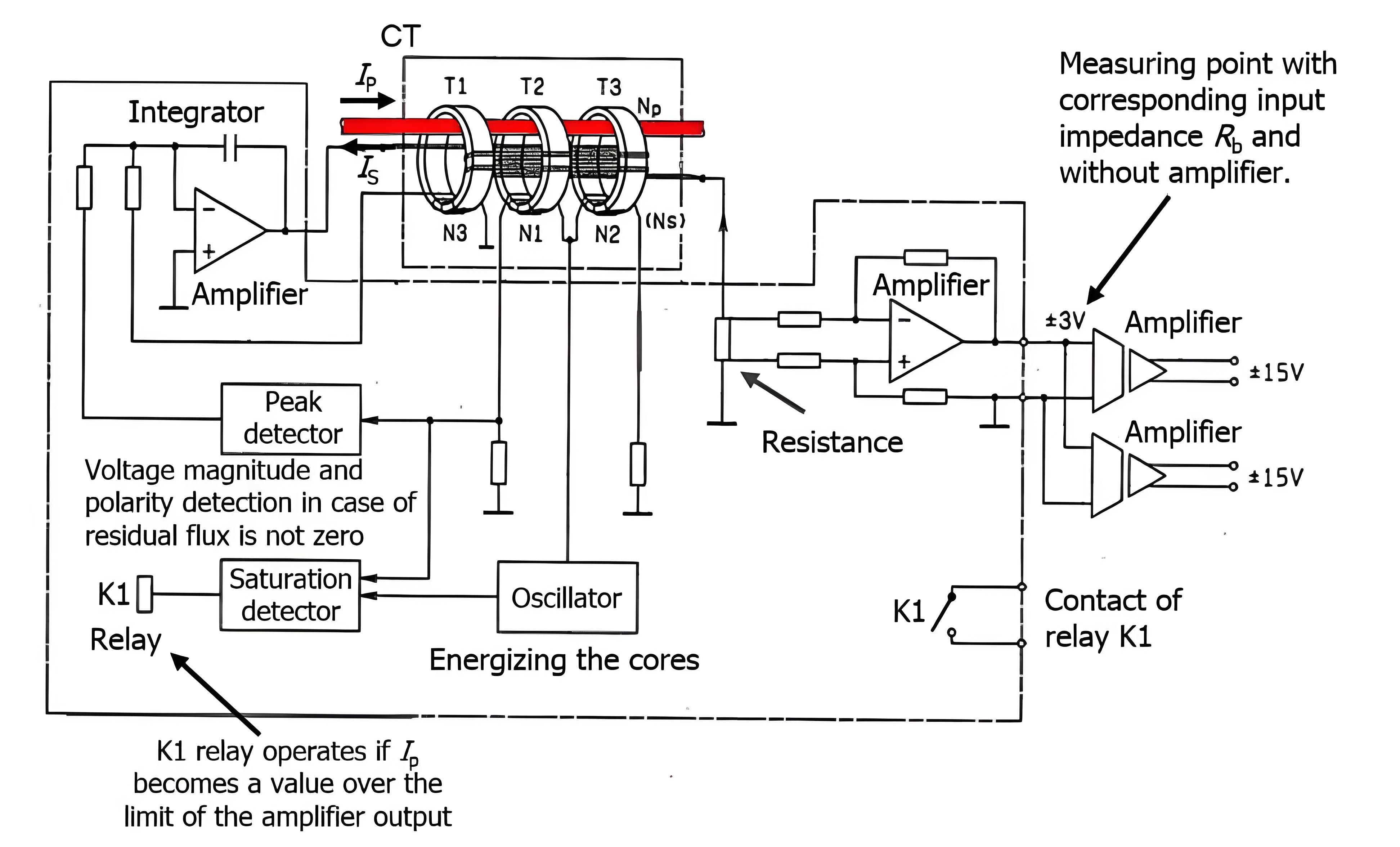
Zero - flux current transformers are precision instruments designed for AC and AC/DC measurements. Currently, they are most commonly used in High - Voltage Direct Current (HVDC) Gas - Insulated Substations (GIS). The measurement principle of an AC zero - flux current transformer is illustrated in Figure 1.