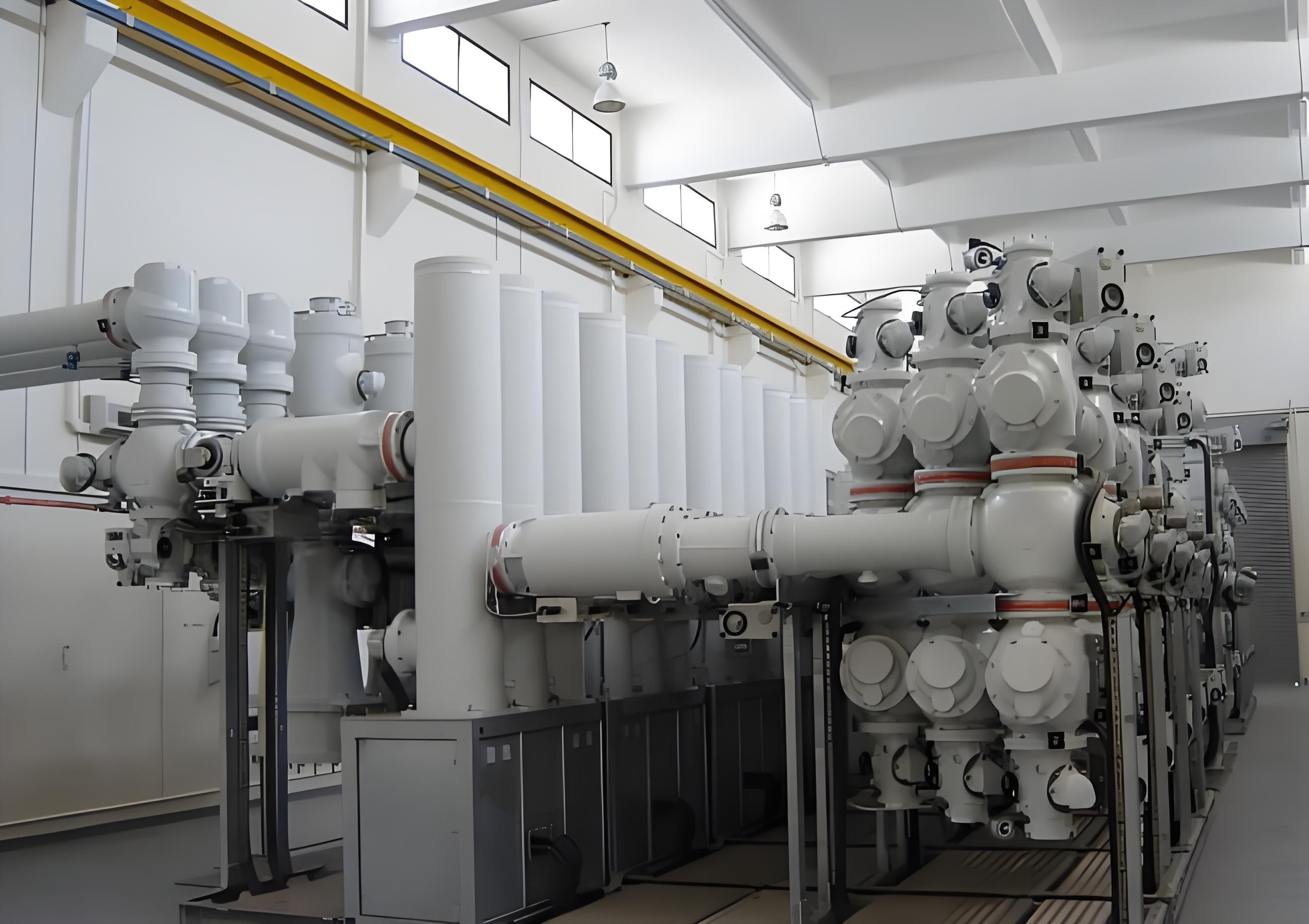
Preventing and controlling SF6 emissions from high - voltage gas - insulated switchgear has long been a formidable challenge.Here, you can find more details about the key points of on - site SF6 gas leakage tests for high - voltage switchgear.Sulphur Hexafluoride (SF6) emissions from electrical equipment have been a major concern in the pursuit of greenhouse gas emission reduction goals. This is because SF6 emissions have a substantial impact on global warming. SF6 has an atmospheric lifetime of 3,200 years, and its Global Warming Potential (GWP) is 23,900 (meaning that the impact of 1 kg of SF6 is equivalent to that of 23,900 kg of CO2).In 2000, SF6 emissions from the production of medium - and high - voltage (HV) electrical transmission and distribution equipment were estimated to be around 10 Mt CO2 - eq, mainly concentrated in Europe and Japan.
In the journey towards a net - zero world, it is widely recognized that the power industry has undergone significant transformations, shifting from hydrocarbon - based power generation to renewable and green energy sources. However, an issue that may not be as well - documented is the control of another environmental risk within the industry.
Since the 1950s, Sulfur hexafluoride (SF6) has been used as an insulating and arc - quenching medium in high - voltage switchgear. Due to its inert nature and excellent arc - quenching properties, it is primarily applied in switchgear. Additionally, the chemical composition of SF6 makes it suitable for other uses. For example, in the medical field, it serves as a contrast agent in ultrasound imaging; in double glazing, it functions as a thermal and acoustic insulating medium; and at one time, it was even used as the "air" filler in the sole of a well - known brand of sports shoes.
Ever since the adoption of the Kyoto Protocol in 1997, efforts have been made to limit the use and emissions of SF6. In recent years, remarkable progress has been achieved in the electrical transmission industry in developing alternative equipment and insulating media.
Dry - air insulation can now be utilized for voltages up to 420 kV in non - switching gas - insulated busbars (GIB), and vacuum interrupters have been developed for use at voltages up to 145 kV. Similarly, alternative gas technologies such as g3 (g - cubed) can be applied for voltages up to 420 kV in non - switching gas - insulated busbars (GIB). Alternate gas circuit breakers are available for voltages up to 145 kV, and it is anticipated that scalable 245 kV g3 circuit breakers will be accessible by 2025.
Nevertheless, considering the normal operating lifespan of high - voltage GIS, which is 25 years or more, and the fact that almost all currently manufactured high - voltage GIS are filled with SF6, the environmental impact of SF6 remains an issue that needs to be addressed not only now but also in the coming decades. Moreover, with the progress in extending equipment lifespan through predictive maintenance, the environmental cost of replacement should also be taken into account. A gas leak in otherwise healthy equipment does not necessarily mean that replacement is required.
Gas leaks in high - voltage GIS occur for various reasons, including manufacturing defects, design flaws, the impact of weather on outdoor equipment, incorrect installation, and the aging of gaskets and seals. Given the critical nature of many substations, the ability to shut down equipment for repair is often restricted. This can lead to a continuous need to top up leaking gas zones, resulting in a constant equivalent emission of SF6 gas into the atmosphere.
In many regions worldwide, governments and regulators not only impose severe penalties for such emissions but also provide incentives for managed reduction. Therefore, there is a demand for an effective solution to gas leaks that can prevent SF6 emissions from aging equipment, without relying on the operationally disruptive and time - consuming conventional OEM approach of shutdown, degassing, dismantling, and repair.
In recent years, several methods have been attempted, but with limited success. These methods often only reduce rather than completely solve the leak problem and may also restrict future access to the affected components.
- Adhesive Coatings or Industrial Wraps: When applied directly to the leaking area under pressure, adhesive coatings or industrial wraps fail to stop leaks. Even with a reduction in gas pressure and the associated operational disruption during installation and curing, the success rate is usually limited and short - term.
- Epoxy Encasings: Epoxy encasings can redirect the leak during the curing process, successfully avoiding the problem in the first method and stopping the leak. However, the limitations of this method include being generally restricted to flange locations. Moreover, the finished product solidifies onto the equipment, restricting future access if necessary. Removal is time - consuming, and extreme caution must be exercised to avoid damaging the encased flange and bolts during the process.
MG Eco Solutions (Master Grid Group) has developed a unique system that overcomes the major limitations of operational disruption, restricted leak - location application, and inconsistent success rates. This system was initially developed for use in the harsh environment of French coastal nuclear power stations and has also proven effective in tropical climates.
In Photo 1, you can view MG Eco Solutions' Sleakbag collection system for high - voltage gas - insulated switchgear.
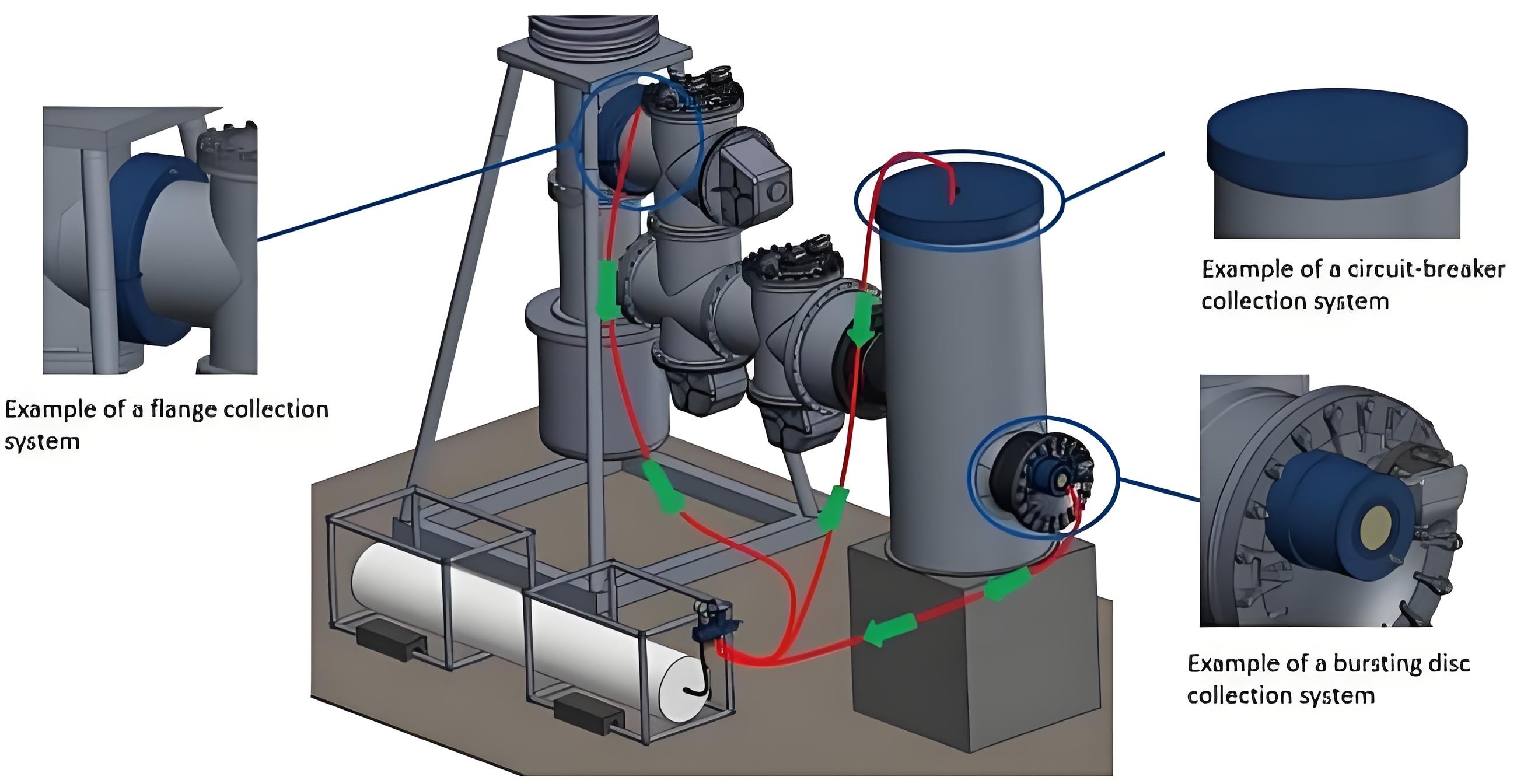
Through a meticulous reverse - engineering process, MG Eco Solutions has the capability to design and manufacture containment systems tailored to address gas leaks in nearly any location on any brand of Gas - Insulated Switchgear (GIS).
The company's solution combines a novel gas - tight polymer seal and O - ring. Instead of attempting to plug the leak directly or fill the void with resin, it contains the gas leak within the system. The containment system can be regarded as a permanent fix. However, it is also removable when access to the equipment becomes necessary, and some components are designed to be reusable in other applications.
What further enhances the versatility of MG Eco Solutions is its ability to offer a collection system in situations where a permanent containment system is unfeasible, such as in the case of a leaking bursting disc or bellows unit. This solution adheres to the same reverse - engineering principle to ensure a precise fit with the leaking equipment. Instead of containing the leak under working pressure, the gas is diverted through pipes to a collection system, thus preventing the harmful SF6 emissions from entering the atmosphere.
The power industry's long - term aspiration towards a net - zero world is the complete phasing - out of SF6 - filled equipment. Achieving this goal demands time, substantial investment, and continuous progress in alternative technologies. In the interim, effectively managing the extensive existing installed base of GIS and implementing containment and collection measures for SF6 gas leaks represent crucial contributions to this overarching objective.
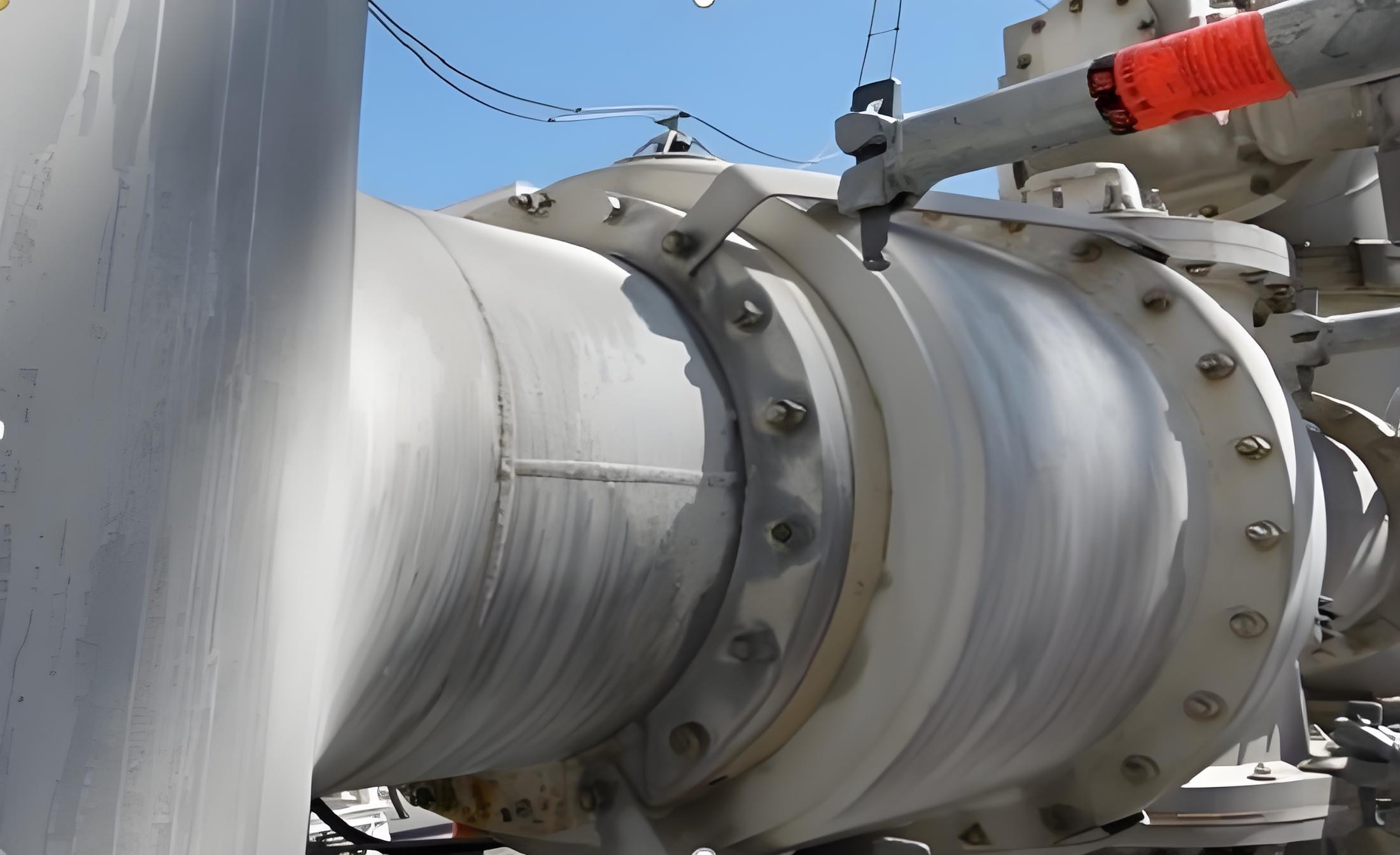