As a frontline tester, I work with industrial and commercial energy storage systems daily. I know firsthand how critical their stable operation is for energy efficiency and business profitability. While installed capacity grows rapidly, equipment failures increasingly threaten ROI—over 57% of energy storage plants reported unplanned outages in 2023, with 80% stemming from equipment defects, system anomalies, or poor integration. Below, I share practical testing insights for the five core subsystems (battery, BMS, PCS, thermal management, EMS) and three - tiered inspection framework (daily checks, periodic maintenance, deep diagnostics) to help fellow practitioners.
1. Core Subsystem Testing Practices
1.1 Battery System: The "Heart" of Energy Storage
Batteries are the energy backbone, requiring comprehensive testing across three dimensions:
(1) Electrochemical Performance Testing
- Capacity Testing: Follow GB/T 34131—discharge at 0.2C to cutoff voltage (25±2℃), compare actual vs. rated capacity to assess “endurance.”
- Internal Resistance Testing: Use AC injection (1kHz sine wave, most representative but prone to interference), AC discharge conductance, or DC discharge methods. I recommend enhancing AC injection with Kalman filtering to reduce noise for accuracy.
- SOC/SOH Monitoring: Combine ampere - hour integration, open - circuit voltage, and electrochemical impedance spectroscopy. Modified ampere - hour integration (accounting for temperature and charge - discharge states) keeps SOC errors <1%.
(2) Safety Performance Testing
- Thermal Runaway Testing: Follow UL 9540A—test at cell, module, and system levels to characterize thermal runaway behavior and gas combustion properties (critical for hazard assessment).
- Overcharge/Overdischarge Testing: Simulate extreme conditions per GB/T 36276 to verify safety thresholds.
- Short - Circuit Protection Testing: Directly simulate external shorts to validate protective responses (a must - have for system safety).
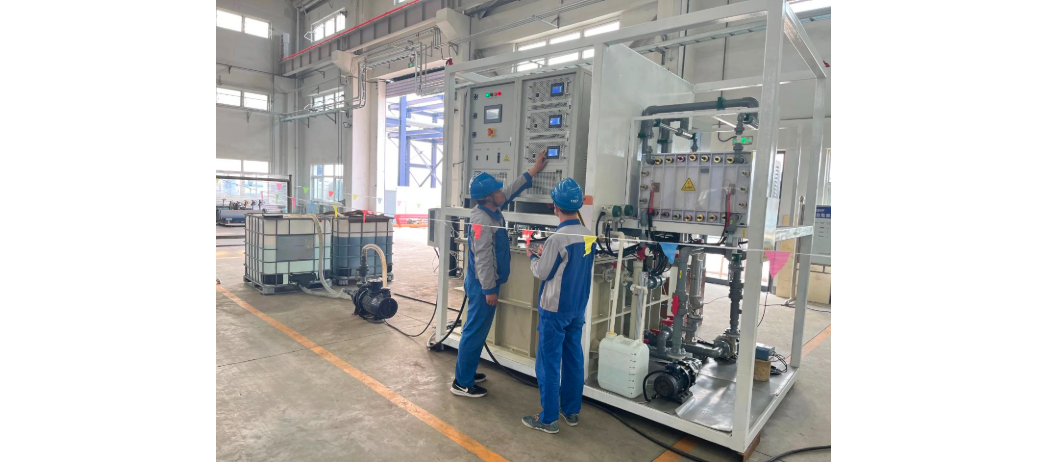
(3) Physical Condition Testing
- Visual Inspection: Check for case deformation, leaks, and legible labeling (small details hide big risks).
- Connector Testing: Inspect for oxidation, corrosion, or looseness; measure contact resistance (poor connections cause operational failures).
- Ingress Protection (IP) Testing: Follow GB/T 4208 to ensure reliability in harsh environments (dust, moisture, etc.).
1.2 BMS: The "Brain" of Battery Management
BMS monitors and protects batteries—focus on communication, state estimation, and protection:
(1) Communication Protocol Compatibility Testing
BMS must integrate with PCS/EMS via protocols like Modbus/IEC 61850. Use CAN analyzers (e.g., Vector CANoe) and protocol converters to test:
- Latency: ≤200ms
- Success Rate: ≥99%
- Data Integrity: No loss/corruptio.
I use finite - state machine (FSM) - based test case generation to cover all communication scenarios.
(2) SOC/SOH Algorithm Validation
Ensure SOC errors ≤±1% and SOH errors ≤±5% (GB/T 34131):
- Offline Calibration: Compare BMS estimates to lab - measured capacity / Internal Resistance
- Online Testing: Simulate real - world charge - discharge cycles.
- Battery simulators and BMS interface emulators automate this for efficiency.
(3) Cell Balancing Testing
- Active Balancing: Simulate cell mismatches to validate BMS strategies.
- Passive Balancing: Track long - term mismatch trends.
Use results to judge if balancing meets system needs.
(4) Safety Protection Testing
Trigger overcharge, overdischarge, and thermal protection:
- Example: Overcharge test—continue charging a full battery to verify BMS disconnects the circuit.
Must meet GB/T 34131 requirements.
1.3 PCS: The "Power Hub" for Energy Conversion
PCS converts AC/DC—test efficiency, protection, and power quality:
(1) Efficiency Testing
Meet GB/T 34120 (≥95% efficiency at rated power):
- Input - Output Comparison: Measure power at both ends to calculate efficiency.
- Load Profiling: Test across loads to map efficiency curves.
Use high - precision analyzers (e.g., Fluke 438 - II) at 25±2℃ for accuracy.
(2) Protection Testing
Validate overload (110% rated load), short - circuit, and overvoltage responses. Must meet GB/T 34120.
(3) Harmonic Analysis
Ensure THD ≤5% (GB/T 14549/GB/T 19939):
- Direct Measurement: Use power quality analyzers (e.g., Fluke 438 - II) to test waveforms.
- FFT Analysis: Calculate harmonic amplitudes from current signals.
- Test across loads and operating conditions.
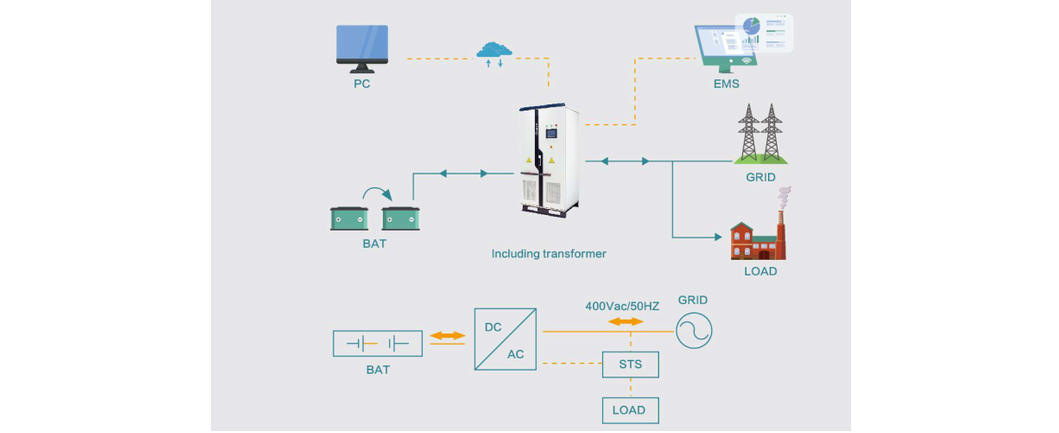
(4) Output Stability Testing
Measure voltage, frequency, and power factor stability under varying loads. Use high - precision scopes/analyzers to verify compliance.
1.4 Thermal Management System: The "Cooling Guardian"
Maintains optimal battery temperature—test cooling, temperature control, and ruggedness:
(1) Cooling Performance Testing
- Air - Cooled Systems: Test filter clogging (pressure drop) and fan life (vibration analysis).
- Liquid - Cooled Systems: Test pipeline pressure (hydraulic sensors) and coolant flow (flowmeters).
Must meet GB/T 40090. Example: CATL uses modified K - means clustering + wavelet denoising to predict SOH with <3% error.
(2) Temperature Control Precision Testing
- Uniformity: Deploy sensors across the battery pack, ensure max ΔT ≤5℃ (GB/T 40090; liquid - cooled systems target ≤2℃).
- Response Time: Measure time to stabilize temperature after environmental changes.
(3) Ruggedness Testing
Conduct IP (GB/T 4208), vibration (GB/T 4857.3), and salt - spray (GB/T 2423.17) tests. Critical for extreme environments (e.g., Huawei’s Red Sea project uses distributed cooling for 50℃ conditions).
(4) Leak Detection (Liquid - Cooled Only)
- Fluorescent Tracer: Add dye, inspect with UV light.
- Pressure Testing: Pressurize lines to check seals.
- Ensure no leaks and stable coolant pressure.
1.5 EMS: The "Commander" of Energy Management
Optimizes operation and dispatching—test algorithms, communication, and security:
(1) Algorithm Accuracy Testing
Validate load forecasting, charge - discharge optimization, and economics:
- Historical Backtesting: Use past data to verify models.
- Live Testing: Validate with real - time operations.
- Example: CATL’s AI cuts fault detection time by 7 days, boosting efficiency by 3% and reducing losses by 25%.
(2) Communication Protocol Compatibility Testing
Ensure support for IEC 61850/Modbus (IEC 62933 - 5 - 2):
- Conformance Testing: Verify compliance with standards.
- Interoperability Testing: Test integration with BMS/PCS.
(3) Data Security Testing
Validate SM4 encryption, access control, and integrity (per national crypto standards):
- Encryption: Test SM4 key exchange.
- Access Control: Verify user permission enforcement.
- Integrity: Ensure no data loss/corruption during transit/storage.
(4) Response Time Testing
Ensure system response ≤200ms (GB/T 40090) to handle grid demands. Trigger EMS actions and measure latency.
2. Three - Tiered Inspection Framework
2.1 Daily Checks (Rapid Fault Detection)
Conducted per shift to catch issues early:
- Scope: Battery temp/voltage/SOC, BMS communication, PCS parameters, thermal cooling, EMS data.
- Tools: Thermal cameras, multimeters, oscilloscopes, communication testers.
- Focus: System status and anomalies—address issues immediately.
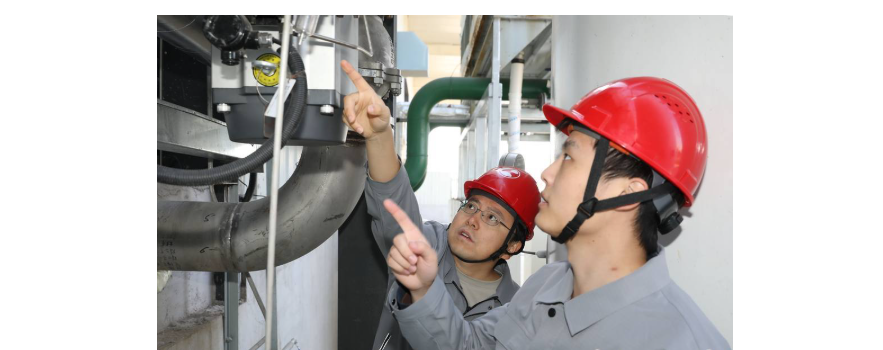
2.2 Periodic Maintenance (Preventive Care)
Scheduled to extend lifespan:
- Scope: Battery internal resistance (AC injection), BMS firmware updates/SOC calibration, PCS efficiency/harmonics, thermal system seals/IP, EMS algorithm updates/security checks.
- Tools: Dedicated resistance meters, CAN analyzers, power analyzers, encryption tools.
- Cadence: Tailor to equipment (e.g., quarterly battery tests, semi - annual BMS updates).
2.3 Deep Diagnostics (Root - Cause Analysis)
Triggered by recurring issues (e.g., frequent thermal runaway alerts, BMS communication failures):
- Scope: Thermal runaway (UL 9540A), BMS fault diagnosis, PCS protection/efficiency deep dives, thermal system leak/vibration tests, EMS algorithm validation/security scans.
- Tools: Thermal runaway chambers, vibration analyzers, encryption scanners, fault injectors.
- Goal: Identify root causes for targeted repairs/upgrades.
3. Best Practices: Standardization, Data - Driven Testing, Prevention
3.1 Standardization
Follow IEC 62933 - 5 - 2/GB/T 40090 - 2021:
- Process: Define preparation (scope, tools, environment), execution (testing + data logging), and analysis (reporting).
- Reports: Include equipment specs, test conditions, data, results, and recommendations (per GB/T 40090 requirements for traceability).
3.2 Data - Driven Testing
Build a unified data pipeline (battery temp, voltage, SOC, PCS efficiency, THD, etc.). Use AI (LSTM, random forests) and digital twins:
- Example: CATL’s AI predicts SOC errors <1% and SOH decay with >95% accuracy, issuing 7 - day advance thermal runaway alerts.
- Example: Huawei uses digital twins to simulate extreme conditions, pre - identifying failures.
3.3 Preventive Testing
Schedule proactive checks based on equipment behavior:Cadence: Quarterly cell balancing, semi - annual BMS updates, annual PCS harmonics/thermal seals checks, quarterly EMS algorithm updates.
- Triggers: Deep diagnostics for ≥5% internal resistance rise (3 consecutive tests) or recurring communication failures.
Frontline testing demands rigor, expertise, and practical know - how. Mastering these subsystems, tools, and strategies ensures energy storage systems deliver reliability and efficiency—safeguarding business and grid operations. This guide distills years of hands - on experience—I hope it empowers fellow testers to raise the bar in energy storage reliability.